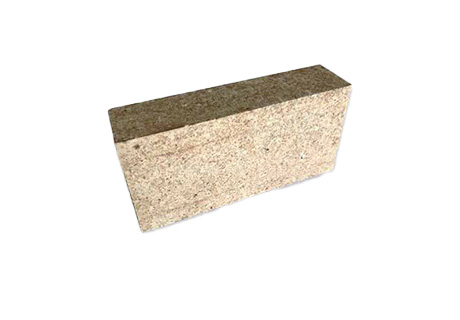
Zircon Brick
1.High temperature resistance & high strength 2.Excellent wear resistance Property 3.Strong slag resistance, especially acidic slag 4.High temperature volume stability 5.Excellent thermal shock resistance 6.Small thermal expansion rate 7.High bulk density and low porosity 8.Resistance to molten steel and glass solution 9.Thermal conductivity decreases with increasing temperature
Brief Introduction
High dense zircon block consists of two kinds of bricks- HDZ-65 and HDZ-68. Characterized by high bulk density, low apparent porosity, mechanical strength, excellent stability of thermal shocking and resistance to corrosion of glass liquid under load, it is mainly used for soda-lime glass kiln, channel blocks as well as sidewall of glass fiber kilns and floating glass tanks.
Zirconia Brick is manufactured using high quality zirconia and zirconium corundum clinker raw materials with ceramic and chemical bonding.Zirconia brick is shipped under high pressure and fire with high temperature with scientifically and reasonably gradating and adding good performance of additives.
Technical Datas
Item/Index | ZR-30 | ZR-50 | ZR-55 | ZR-60 | ZR-62 | |
Al2O3 % | 42 | 10 | 6 | 4 | – | |
SiO2 | 20 | 34 | 35 | 30 | 34 | |
ZrO2 | 30 | 50 | 55 | 60 | 62 | |
Bulk Density (g/cm3) | ≥3.10 | ≥3.30 | ≥3.45 | ≥3.50 | ≥3.60 | |
Apparent Porosity % | ≤21 | ≤20 | ≤20 | ≤21 | ≤20 | |
Compressive Strength (kg/cm2) | ≥500 | ≥400 | ≥500 | ≥500 | ≥500 | |
Refractoriness Under Load ℃ (T2) | >1500 | >1450 | >1500 | >1600 | >1550 | |
Expansion at 1000℃ (%) | 0.6~0.8 | 0.4~0.6 | 0.4~0.6 | 0.4~0.6 | 0.4~0.6 | |
Thermal Conductivity | 500℃ | 1.7 | 1.4 | 1.3 | 1.2 | 1.2 |
1000℃ | 1.8 | 1.6 | 1.5 | 1.5 | 1.5 | |
Application | Glass Furnace | Nozzle Seat | Ladle | Ladle | Ladle Glass Furnace |
Application
Zircon Block For Sale is used for lining of steel drums, lining of stainless steel ladles, continuous lining of steel linings, casting nozzles, plug bricks, sleeve bricks and high-temperature induction furnace linings. Also used for the paving bricks or back walls of the glass kilns and around the feeding mouth can also be used for the serious parts of the glass and bottom of the aluminum smelting furnace.