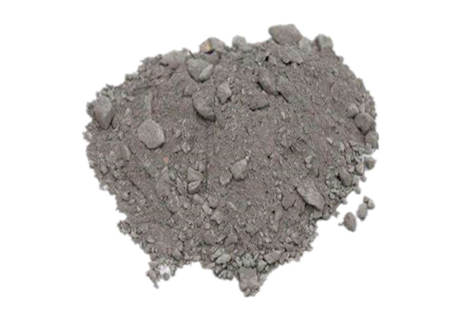
Brief Introduction
Alkali-resistant castables belong to the aluminum silicate series acidic refractory castables. It is a mixture of alkali-resistant refractory aggregates and powders, binders and admixtures. It can resist alkali metal oxides (such as K2O and Na2O) erosion. A crust anti-corrosion protective layer will be formed on the surface at a temperature of 1250°C. It can effectively prevent the erosion and penetration of the cast body by the alkaline airflow and materials in the cement kiln material at high temperature.
Technical Datas
Items | High Strength Alkali Proof Castable | ||
RW-13NL | RW-14N | ||
Chemical Composition % | Al2O3 | 48 | 45 |
Bulk Density g/cm 3 | 110℃x24h | 2.2-2.4 | 2.2-24 |
MOR MPa | 110℃x24h | 7 | 8 |
1110℃x3h | 7 | 8 | |
Cold Crushing Strength MPa | 110℃x24h | 70 | 80 |
1110℃x3h | 70 | 80 | |
Linear Dimensional Change% | 1110℃x3h | ±0.4 | ±0.4 |
Maximum Service Temperature ℃ | 1300 | 1400 |
Application
Alkali-resistant castables can be used in industrial furnaces with alkali corrosion in industries such as iron and steel, nonferrous metals, glass, machinery, and petrochemical industries. Lightweight alkali-resistant refractory castables are mainly used for the top cover of the preheater, cylinder body and thermal insulation lining of the above-mentioned rotary kiln. The heavy alkali-resistant castables are mainly used in the kiln tail, kiln head, preheater, discharge port, tuyere and other parts of the roasted alumina rotary kiln and cement rotary kiln.