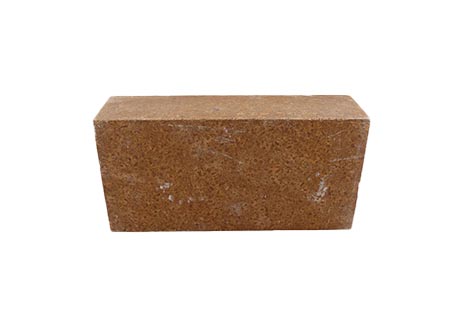
Magnesia Refractory Brick
High refractoriness above 2000°C Excellent alkaline slag erosion resistance Volume stability at high temperature Excellent anti-oxidation Hugh Refractoriness under load about 1500-1550°C High initial load softening temperature Poor thermal shock resistance Good thermal conductivity
Brief Introduction
Magnesia bricks are basic refractory brick materials whose MgO content are more than 90% and adopt periclase as the principal crystalline phase. Magnesia bricks generally can be classified into sintered magnesia bricks (also known as fired magnesia bricks) and chemically bonded magnesia bricks (also known as non-fired magnesia bricks).
Magnesia bricks are featured with high refractoriness, good resistance to alkaline slag, high refractories under load, but poor thermal shock resistance. Magnesia bricks are mainly used in steel-making alkaline furnace, electric furnace hearth and furnace wall, permanent lining of oxygen converter, non-ferrous metal smelting furnace, high-temperature tunnel kiln, calcined magnesia brick and cement kiln lining, glass kiln regenerators checker bricks,etc.
Technical Datas
Index/Item |
Magnesia Refractory Brick |
|||
MgO% ≥ |
91 |
93 |
95 |
97 |
SiO2% ≤ |
– |
3.5 |
2.0 |
1.0 |
CaO% ≤ |
3.0 |
2.0 |
2.0 |
– |
Cold Crushing Strength /MPa≥ |
60 |
60 |
60 |
60 |
Apparent Porosity /%≤ |
18 |
18 |
16 |
16 |
0.2 MPa Refractoriness Under Load / ≥ |
1560 |
1620 |
1650 |
1700 |
Reheating Linear Change (1650℃*2h)/% |
0~-0.4 |
0~-0.4 |
0~-0.3 |
0~-0.2 |
Classicification
In the classification of magnesia bricks by the American Society of Materials and Testing Standards ASTM C 455-1984, magnesia bricks are classified into three grades based on the content of MgO: 90、95、98. The corresponding minimum of MgO are 86%、91% and 96%.
According to the manufacturing process, magnesia bricks can also be classified into fired magnesia bricks, non-fired magnesia bricks and rebonded magnesia bricks.
Magnesia bricks with high purity and high firing temperature are called direct bonded magnesium bricks due to direct contact of periclase crystals; bricks made from fused magnesia as raw materials are called fuse-rebonded magnesium bricks.
Application
1. Iron & steel industry steelmaking linings, ferroalloy furnaces, and mixed iron furnaces
2. Non-ferrous industrial furnaces smelt copper, lead, tin, zinc linings
3. Glass industrial regenerators grids body heat exchanger
4. Refractories industrial tunnel kiln and high temperature firing kiln,etc
5. Building Materials Industry kiln